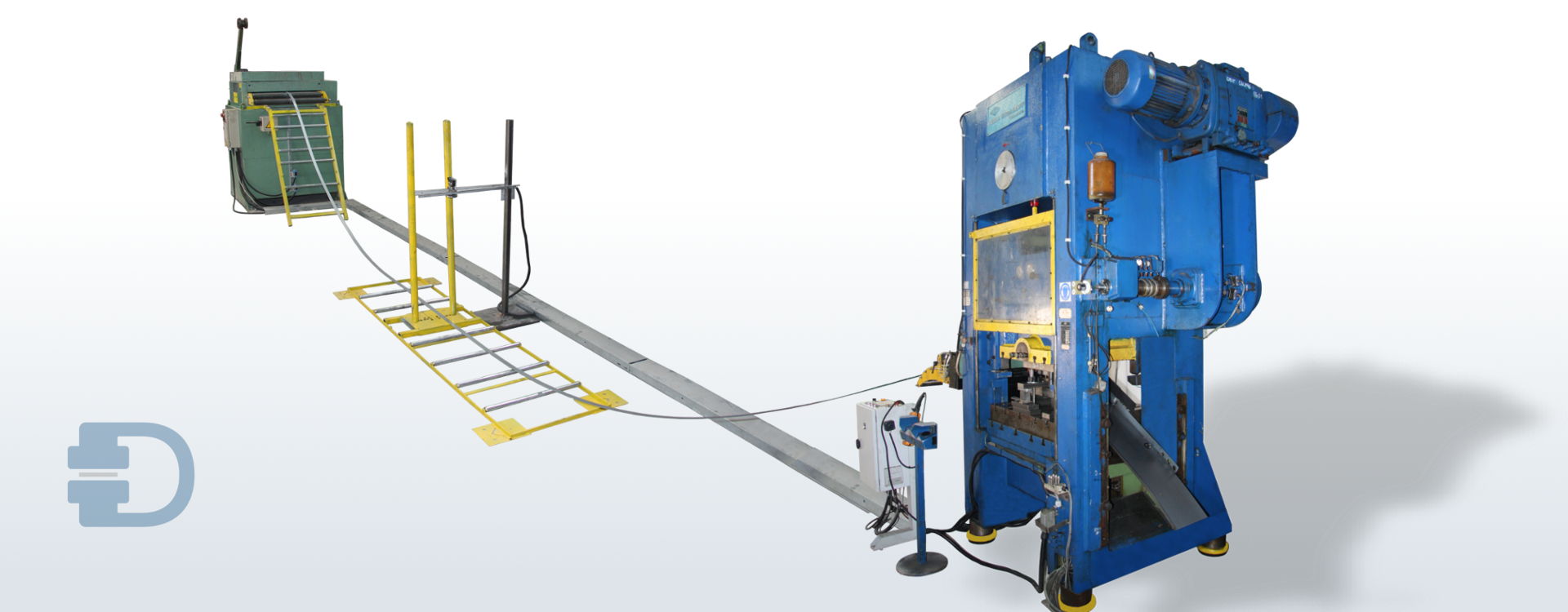
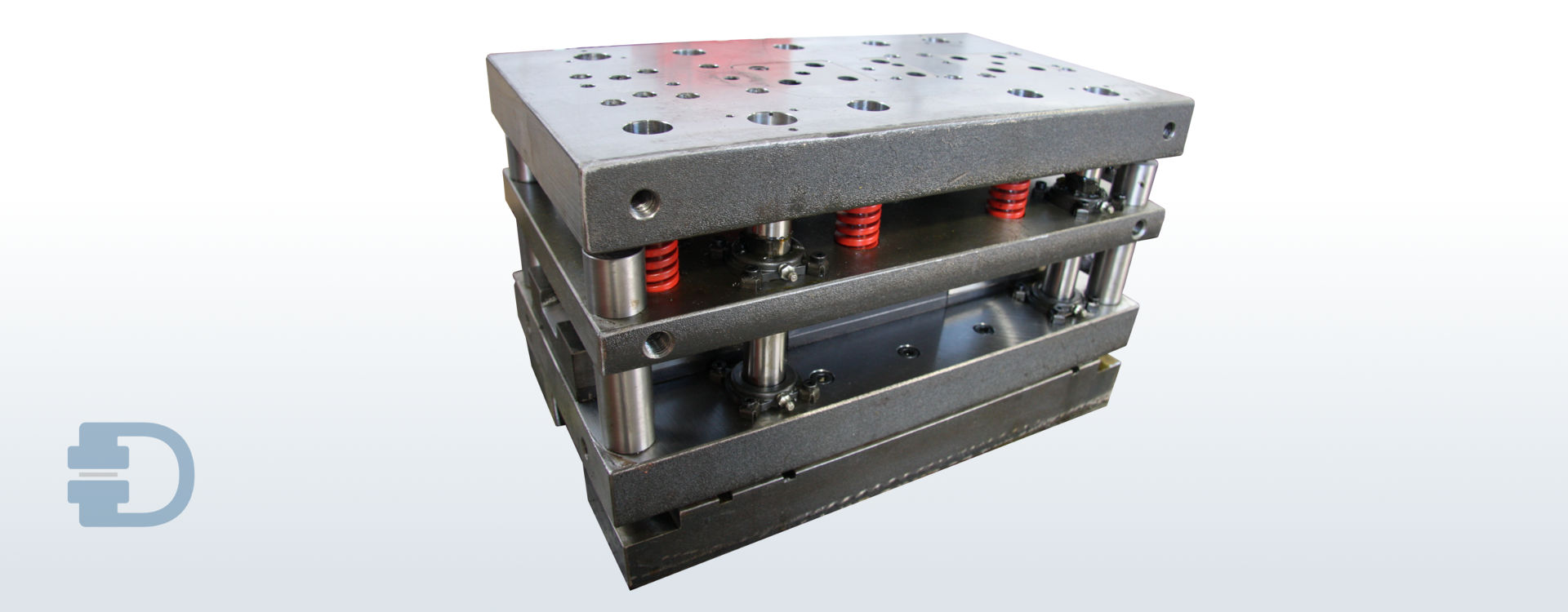
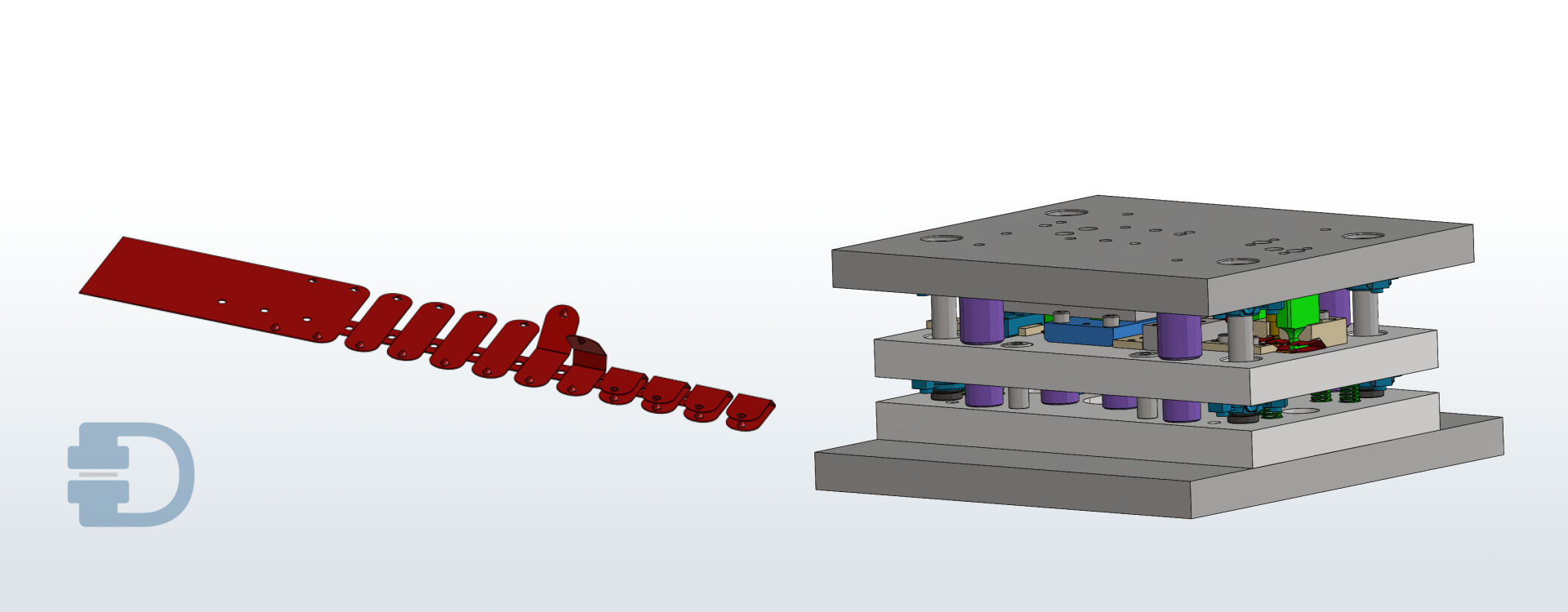
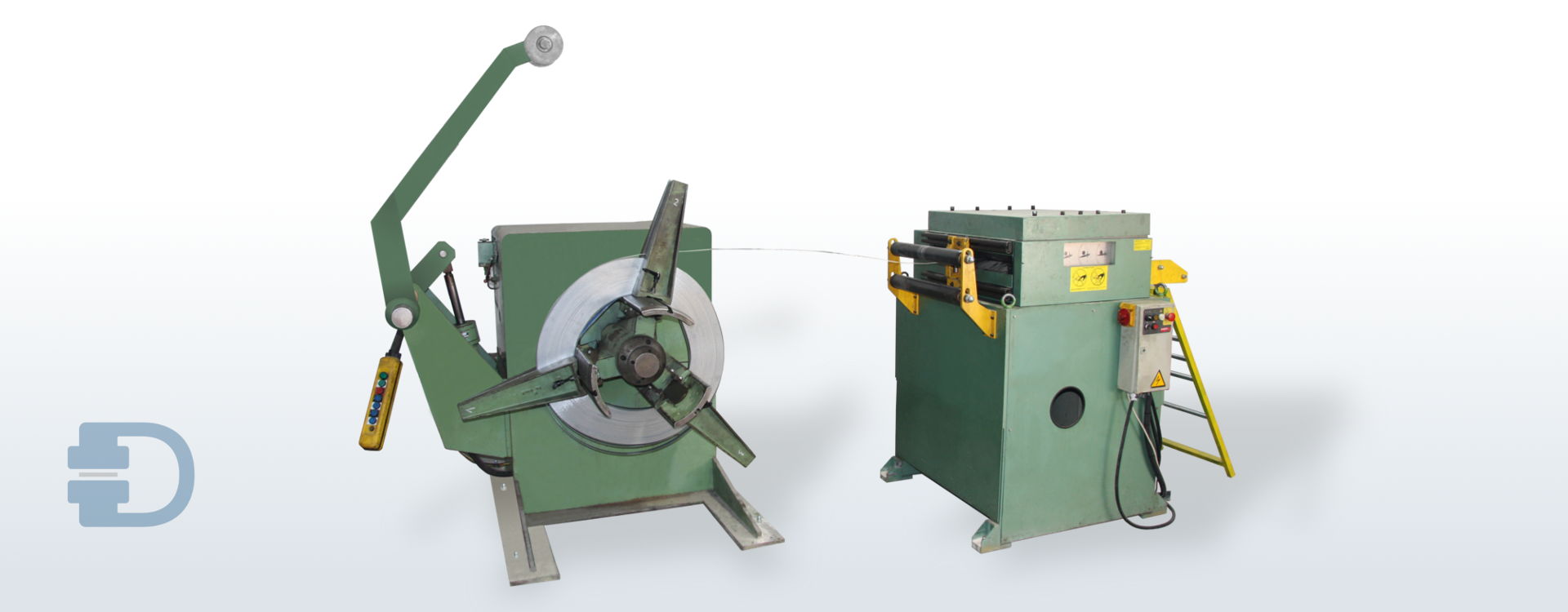
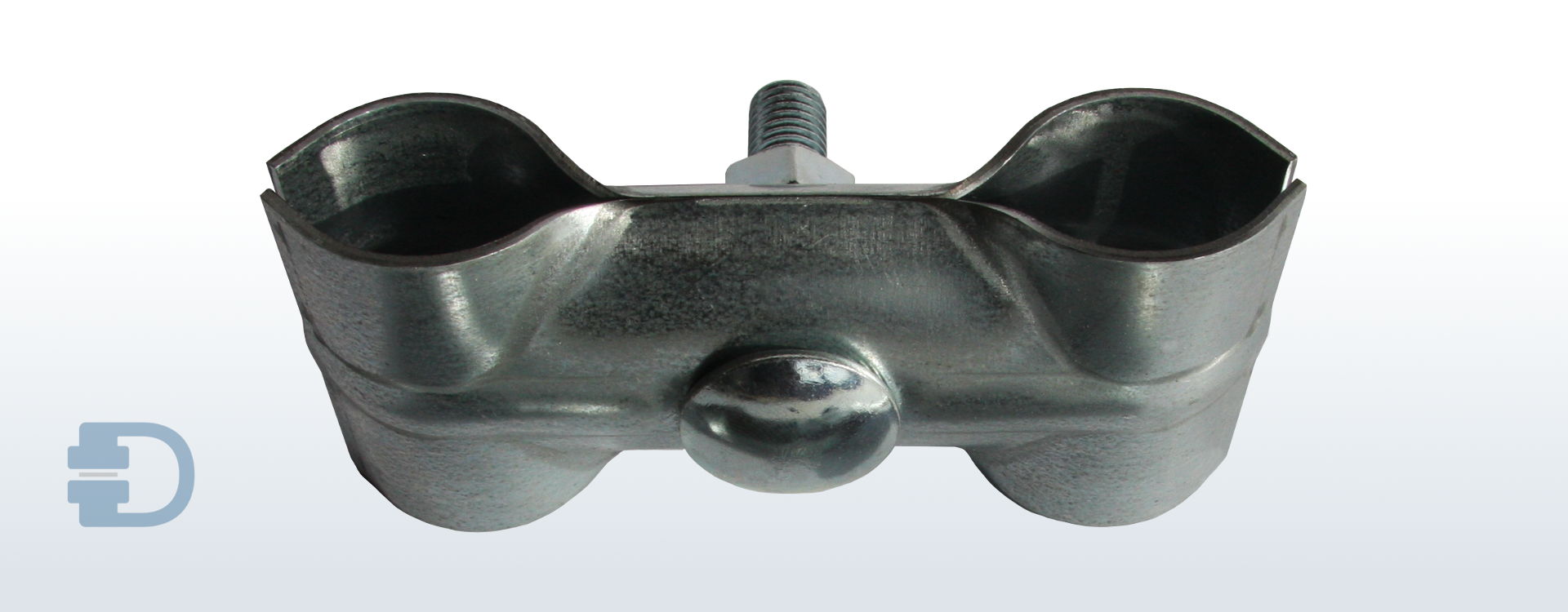
About us
DAKAFORM, S. R. O.
DAKAFORM s.r.o. was founded in February 2015 as a family company focusing on the production and development of pressed parts and tools for cold forming. Our key motivation is to offer all our customers top services and comprehensive support in this area and thus permanently contribute to sustainability and prosperity and customer-supplier relationships.
We have a vision to be a lean company, maximally oriented to meet customer requirements.
Our goal is to produce products with a reasonable margin that will allow us to grow continuously and invest in our production facilities, in order to provide customers with the maximum possible portfolio and service.
Our company is certified according to ISO 9001
Production possibilities and scope
Our company offers the production of cold-formed parts in a wide range of processed materials.
We can process materials from 0.2 mm to 8 mm thick in the form of coils, sheets or rods
- cold rolled carbon steel
- stainless steel sheets and coils
- aluminum and copper coils, sheets and blanks
- nickel coils
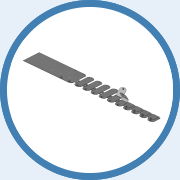
Progressive Stamping
It is a very effective industrial cold forming method designed for the production of parts in series from tens of thousands to millions per year. The input material is always a coil of the necessary material quality and dimensions.
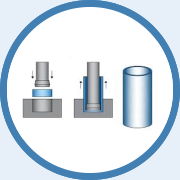
Aluminium impact extrusion
Impact extrusion is a manufacturing process similar to extrusion and drawing by which products are made with a metal slug. The slug is pressed at a high velocity with extreme force into a die or mould by a punch.
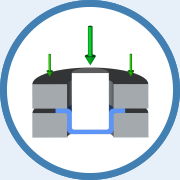
Deep Drawing
Deep drawing is a sheet metal forming process by which a sheet metal blank is slightly clamped along its perimeter by a blank holder and radially drawn into a forming die by use of a punch without intentionally changing the thickness of the sheet.
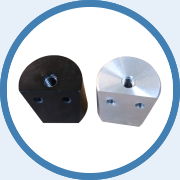
Surface finish and finishing operations according to customer´s requirements
Degreasing, Zinc coating, Cataphoresis (KTL), Powder coating
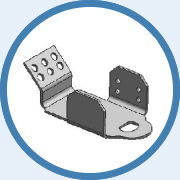
Production of stamped parts in tools with manual insertion
This is the basic production method of stamped parts always using human force to handle parts and control the machine. As a rule, it is used for smaller series of shaped parts where it does not have the economic effect to invest in sophisticated tools and replace human work by robots or transfer and handling automats.
Product gallery
-
Clamping bracket
Material: steel strip S355 thickness 4 mm
Building industry -
Gate hinge
Material: galvanized th. 3 mm
Construction industry -
Bracket
Stamping
Material: stainless grade 1.4301 thickness 1 mm
Building industry -
Clamp for mobile fences
Progressive stamping +manual assembly
Material: zinc coated strip S250GD tlhickness 2 mm
Building industry -
Steel fence bracket
Material: zinc coated strip thickness 2 mm
Building industry -
Heating tube holder
Stamping+bending and assembly
Material: zinc coated strip DX51D thickness . 2 mm
Heating industry -
Door hinge
Stamped part
Material: steel plate thickness 3 mm
Heating industry -
Bracket for positionig
Progressive stamping
Material: zinc coated strip S250GD thickness 2 mm
Building industry -
Holder
Cutting and bending tool
Material: steel sheet th. 3
Heating and heating industry -
Bracket
Stamping
Material: zinc coated strip S250GD thickness 1 mm
Building industry -
Tube holder
Stamped part
Material: steel plate grade S355 thickness 6 mm
Agriculture -
Covering plate
Material: steel plate tlhickness 4 mm
Heating industry -
Deepdrawn rack feet
Deepdrawing
Steel grade S235 thickness 4 mm
Racking industry -
Bracket
Progressive stamping
Material: zinc coated strip thickness 1 mm
Building industry -
Door plate
Stamped part
Material: steel strip thickness 3 mm
Furniture industry -
Bracket for plastic boxes
Progressive stamping
Material: zinc coated strip thickness 0,7 mm
Racking industry -
Reinforcement tube
Material: zinc coated strip from 1 up to 3 mm
Building industry -
Tip plate for magnet
Progressive stamping
Material: tin plated strip thickness: 0,2 mm
Advertising industry -
Stamped part for racking
Stamped part
Material: steel strip S355 thickness 5 mm
Racking industry -
Stamped part
Progressive stamping
Material: stel strip garde S355 thickness 4 mm
Building industry -
Deep drawn laboratory can
Deepdrawing
Nickel strip Ni 99,5% thickness 0,2mm
Laboratory industry -
Nut
Progressive stamping
Flat steel th. 8 mm grade S235
Automotive industry -
Steel innsert for automotive roof window
Progressive stamping
Material: steel strip DC01 thickness: 1,2 mm
Automotive
Final customer: Webasto
Vehicle: Range Rover -
Stainless hook
Progressive stamping
Material: stainless steel th. 1 mm grade 1.4301
Extrerior blinds for windows -
Welded and machined steel assembly
Material: steel plates from 10 to 80 mm
Mining industry
Machinery
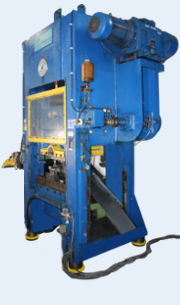
Progressive stamping
line Edelhoff 100
• press force: 10000 kN
• slide stroke: 20-120mm
• press table dimension: 810x860 mm
• number of strokes per minute: 30 - 150
• max. dimensions of coil: 520x3 mm
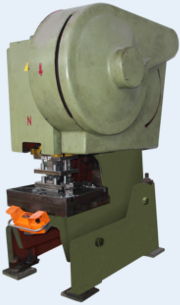
2x Progressive stamping and eccentric press line
Smeral LEN 63C
• press force: 6300 kN
• slide stroke: 20-120mm
• press table dimensions : 800x630 mm
• number of strokes per minute: 10 - 160
• max. dimensions of coil: 300x3 mm
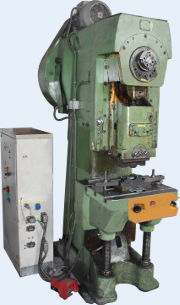
Eccentric press
Weingarten 63
• press force: 6300 Kn
• slide stroke: 20-120mm
• press table dimensions: 700x620 mm
• number of strokes per minute: 120
Other company services
We are also able to provide following services in every phase of your project:
- Pressed parts optimization according to feasibility and cost efficiency
- Prototypes regarding to your drawing
Tools and dies design and dies supply - Production lines design and turnkey projects
- Advisory in a field of cold stamping and deep drawing
Contact
DAKAFORM s.r.o.
Company headquarters: | Rybářská 365 735 62 Český Těšín Czech Republic |
Company registration number: | 038 14 866 |
Company Management
Daniel Kaznica
Executive Director, Project Manager
E-mail: daniel.kaznica@dakaform.cz
Tel.: +420 720 329725
© 2021 DAKAFORM s.r.o.
Tvorba webových stránek Designsoft.cz